Pre-shipment Inspection
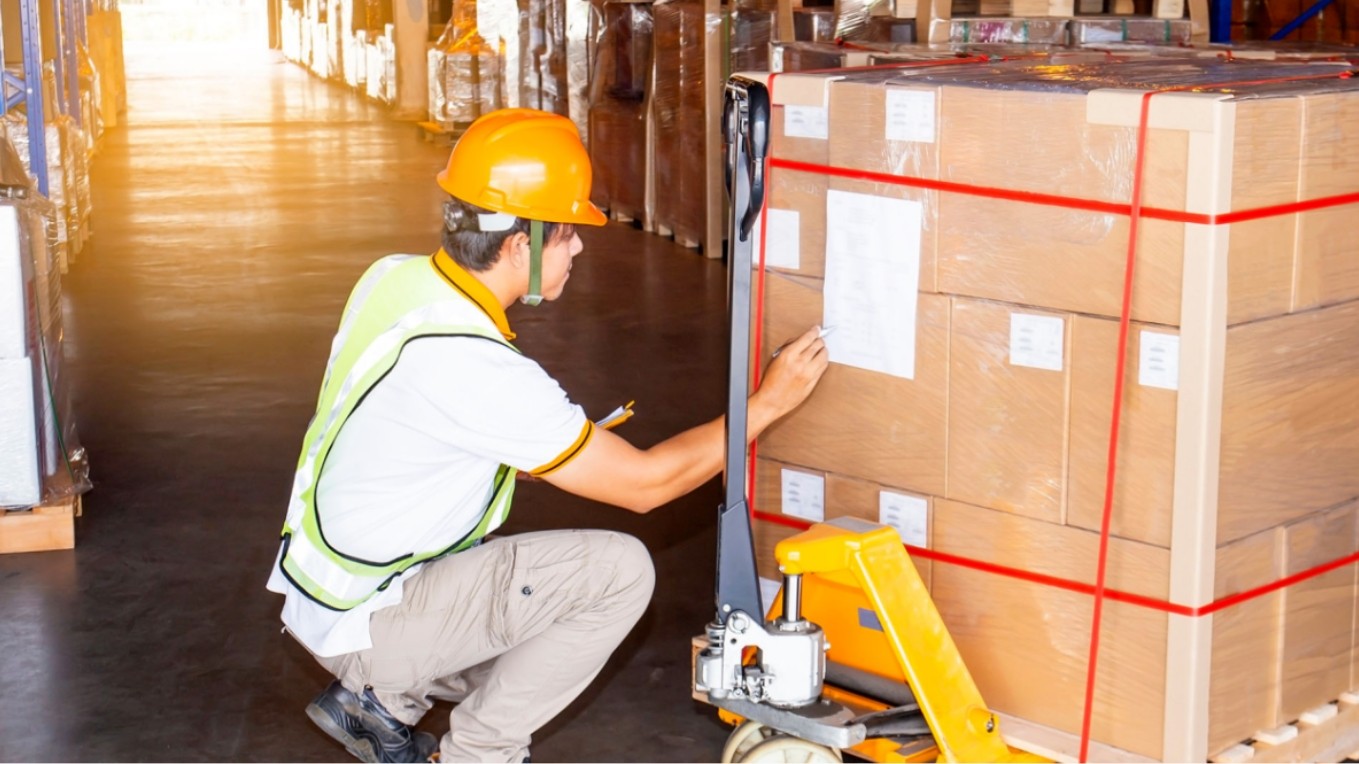
Online shopping has become a very important part of our life. Many merchants and companies have moved their businesses to virtual platforms. This provides ease and convenience to customers and highlights their reputation.
Due to a large number of companies and suppliers offering these services, it can be difficult to compare all of them. It's hard to decide which provider is better. The only basis of comparison we can have is the quality of the products they offer. This is why all companies and suppliers conduct pre-shipment inspections.
They ensure that the items or products they offer are in the correct condition. They need to ensure that fragile products are safe and sound. In order to see all of this, a pre-shipment inspection is required.
What is Pre-shipment Inspection (PSI)?
As we discussed before, pre-shipment inspection is a quality inspection process. Suppliers often hire companies that perform detailed inspections of products. This is done to ensure that the product quality is up to standard. If any product is defective or damaged during this process, it must be replaced or repaired.
This is also done to ensure customers get what they ordered. Many times, suppliers may make mistakes and mix up different orders. The inspection team performs an inventory of the shipped products and orders.
This ensures that customers are satisfied with the delivery. Inspection is a very important step in the whole process. Companies often outsource this service so that it can be done in a proper manner by professionals.
These inspection companies set certain standards or lists of standards. They then match the product to their list of standard conditions. If the condition of the product meets the requirements, the product is approved. Certain procedures and steps are completed during the inspection. Next, we will understand these.
Why Pre-shipment Inspection?
You've probably asked yourself this question many times. Why do I need to spend money on something I can be sure of? No matter how careful you are when sending a product, you can never be sure that it will arrive in the same condition. You should always make sure that the product that the customer receives is as expected.
You should always do this to reduce the risk of errors or mistakes. Spending some money on this service is not a loss. In fact, it is the security of your product. Companies looking to expand their business often take this step. This ensures customer satisfaction. There is no better advertising than advertising that pleases customers.
On the other hand, if your product is defective or damaged, customers will be angry and unhappy. One bad review can change your career. In this case, online profiles can be tainted and flagged with bad feedback. To avoid this, this measure should be taken.
Pre-shipment Inspection Program
Now, let us understand the various steps and stages of pre-shipment inspection. This is a very detailed process and it is important that you understand what your product looks like once it reaches the inspection team. Every company has a different plan of action, but the general gist is the same.
Step 1: Study Visit
This is the first step of inspection. During this period, the hired team visits the production workshop or the products in the factory. This is done on-site.
However, if the product contains any type of potential hazard, access will be conducted off-site. This can be better explained with the help of an example.
Let's say your product is made of a substance that can react with the moisture in something. In such cases, a visit will be made to ensure that the product has not spoiled or deteriorated.
Step 2: Quantity Verification
This step is very simple and straightforward. As the name suggests, this step involves checking and verifying the product quantities in the shipment. The team counts and checks that the number of cartons/boxes is correct.
During this time, they can also check that the packaging is secure and in place. This is quite an important step. Customers often complain about not receiving the right amount of product.
This problem is more common, especially in larger shipments. The team has to check the number of packages to ensure customer satisfaction.
Step 3: Random Selection
This is where the truth about quality is revealed. At this stage, samples are taken from the entire consignment. There are certain standards and limits for the number of defective products in a batch. If the number of defective items exceeds it, the entire shipment is declared defective. If not, the check is passed.
In most cases, this criterion is 80:20: this means that 2 out of 10 items may be defective. If the defective quantity is more than 2 pieces, then reconsider the shipment. In this step, it is decided whether the cargo is healthy or not.
Step 4: Visual and Workmanship Inspection
This is part of the inspection that checks the overall physical condition of the product. This step ensures that the physical appearance and components of the product are properly placed and intact. There are certain types of defects in the product. They are categorized as minor, major, and critical.
Small flaws may go unnoticed. They do not change how the product works. This includes a glitch or question. They are tolerable to a certain extent. On the other hand, there are more major defect issues. These flaws can change and break the way the product is supposed to be. Such deficiencies must be addressed and corrected.
The last one is seriously flawed. A serious defect means that the product poses some kind of danger to its potential consumers. This is a code-red situation and must be avoided at all costs. If the product contains certain sensitive chemicals or ingredients, the visit must be done off-site. This ensures that any critical bugs are kept away from people.
Step 5: Compliance Verification
This step also says it all. In this step, the inspection team checks the order and shipment. They must ensure that the goods conform to the order. This is done in great detail. Let us understand this with the help of an example.
Suppose a buyer orders a batch of pants. Now all kinds of clothing-related orders have to be checked.
Now in a batch of pants, size, and color and everything has to be checked. If you are shipping your phone, you must check the RAM and ROM variants. The colors of the devices must also be checked to verify that they are exactly the colors the customer ordered.
This is also a very important step as it is the key to ensuring customer satisfaction.
Step 6: Functional and Security Testing
This step checks to make sure all products are in order. Check the work and status of the product. No matter what kind of product it is, it needs to go through different stages and steps.
Step 7: Inspection Report
After each test is completed, the inspection team will make a report. This report accurately shows errors or defects in the shipment. If the shipment has only a few minor defects, it is passed.
The report will state in a clear manner that the shipment is approved and ready to go. Conversely, if defects in a shipment exceed a certain point, the report marks the entire shipment as defective.
This report shows everything that came up throughout the inspection.
What is the Pre-shipment Inspection Fee?
This question might pop up in your mind and it might bother you a lot. Is it worth the money to get checked? Before I change your mind, you should know that some countries require PSI. But most people don't, so your skepticism is justified.
Pre-shipment inspection is something you should definitely spend money on. You shouldn't see it as a necessity or something you have to do with discontent.
Think of it as something you're willing to offer your customers. Think of it as a consideration for patronage. You are not the beneficiary of product security. Your client is. Your company's reputation depends on the satisfaction and happiness of your customers.
Therefore, PSI inspection services are very important.
5 Frequently Asked Questions About Pre-shipment Inspection in China
Sellers may experience some issues during PSI. These problems can be caused by a variety of factors. Here, we'll learn about them and the steps we can take to avoid them.
1. Conflict of Interest or Corruption
The question speaks for itself. This happens when your agency or inspector disagrees with you about payment. If you have an agency, you may be overcharged.
Corruption in this matter is very easy for the perpetrators, and there is nothing they can do. The agency may ask you to pay more money than you actually have. Money over and above the bill went straight into their pockets.
This can be done jointly by inspectors or agencies. This is a very serious problem that needs to be addressed.
2. Unclear Inspection Plan
This problem is common in PSI. This is mainly caused by the negligence of the seller. When you wish to inspect your cargo, you have to provide every detail and requirement to the inspection company. If you want an intrinsic check for a certain product, you have to specify it. You must have a clear and transparent plan.
If you don't, the check will yield no results. Bugs and bugs still exist. It's no use spending money on inspections if you're not going to provide the correct instructions and details.
3. Lack of Commitment
This problem is caused by the supplier. Suppliers may show a lack of commitment by not paying due attention to the process. They may overlook important aspects. Let's list some things that count as a lack of commitment so you can avoid them in the future.
- Disagree on specifications; usually dimensions
- Use different raw materials and items
- Failing to determine a time and date for completion
There are many other things that can cause many problems. If anyone is going to be successful and they want their checks to go through smoothly, they have to make the right commitments for it.
4. Lack of Responsibility
This is where things can get very uncomfortable and against you. If the check somehow goes wrong or bugs out, you could be in trouble. You must be vigilant and responsible throughout the process to hold suppliers or inspectors accountable should anything go wrong. If there is a problem with the shipment and you don't realize it until after inspection, the responsibility will fall on you.
Since you've already inspected your shipment, remove the supplier from the equation. Once your inspection passes, the shipment is declared ready to ship. Even if there is something you forgot to check. This carelessness can leave you in a state where you can't do anything about the loss.
5. Maintain the Status Quo
Today, most PSI service providers benefit from establishing a dominant mindset in the minds of their customers. In some places, this is a necessary requirement. If you look at it that way, you might even feel that, because of the way things are done now, the PSI agencies are taking advantage of the status quo to ensure their business thrives. They may even choose to provide poorer service given the demand for their service.
How Can RND Sourcing Help You with Pre-shipment Inspection?
As we have seen before, RND is an excellent company that can help you with the post-shipment and pre-shipment procedures. When it comes to PSI, RND can provide you with simple and efficient inspection services.
RND is a company you can work with confidence. The company can also assist you with follow-up matters.
Frequently Asked Questions About Pre-shipment Inspection
Here are some common questions and questions customers ask about PSI:
When is Pre-shipment Inspection Required?
In most cases, PSI is required when the government requests it. As we discussed earlier, some countries require PSI. Other countries don't require it, but they have certain rules about when it is required.
Who Does the Pre-shipment Inspection and Who Pays for It?
PSI is usually performed by an agency of the importer's choice. These agencies can be found to select the appropriate inspection team and conduct PSI.
In some countries, this is done by the government of the importing country. In the former case, the importer pays for all process costs. In the latter, the government does so.
Who is Responsible for Performing the Pre-shipment Process?
If we were to answer the question quickly, we'd say it's the responsibility of the importer.
But exporters must also take certain steps. There are several legal documents that must be filled out and processed. So it's a mutual activity.
What should I do if there is a problem or disagreement in the pre-shipment inspection?
If you have problems or problems during the inspection, there are two ways you can go about it.
If the target is included in the WTO, certain terms and conditions must be followed. If not, then you can resolve the issue diplomatically.
Are There Additional Certification Checks for Produce and Food?
Yes, there are several examples of such files. If you are sending or receiving grain and such edible products, you must collect certain documents.
These documents show that the product is safe and hygienic. There are specialized agencies, such as FGIS (Federal Grain Inspection Service), that only inspect grains and food products.
In Conclusion
Pre-shipment inspection is an important step that product quality inspection must complete. There are several procedures and processes that must be completed during PSI. You have to be vigilant throughout the event so you can avoid problems of all kinds.
There are some reputable companies that can reliably provide you with the best service. We've also cleaned up some common issues further. If you are looking for a Chinese agent purchasing company to help you with pre-shipment inspection, welcome to contact us.
RND is a professional China product purchasing agent that can help you with product inspection and complete the shipping and purchasing process. We are a purchasing agent, which means we can help you to lower the price. 6 years ago, we started to cooperate with Amazon and Shopify sellers in product sourcing, development, inspection, bundling, packaging, manufacturing, supplier management, FBA shipping, etc. With our help, more and more of their products become Amazon's top picks and bestsellers.